Unlocking Efficiency: How a WMS Transforms Warehouse Operations
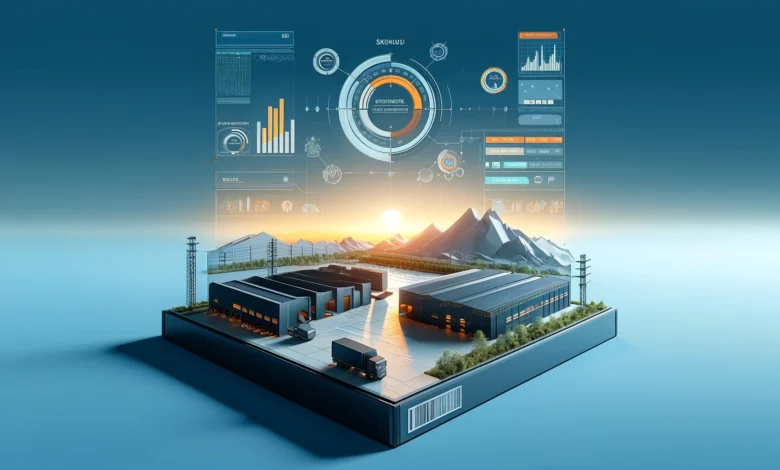
In the fast-paced world of logistics and distribution, warehouse operations play a critical role in the smooth functioning of the entire supply chain. With the demand for quicker turnarounds, reduced costs, and better accuracy, businesses are increasingly turning to technology to optimize their warehouse operations. One of the most effective tools in this regard is a Warehouse Management System (WMS). This powerful software solution is designed to automate, streamline, and enhance various warehouse processes, unlocking significant efficiency improvements. In this blog article, we will explore how a WMS transforms warehouse operations and why it has become indispensable for businesses looking to stay competitive in today’s market.
Understanding the Role of a Warehouse Management System (WMS)
A Warehouse Management System (WMS) is software used to manage and optimize the operations of a warehouse. It provides real-time data about inventory levels, order status, stock locations, and more, helping warehouse managers to make informed decisions and efficiently manage day-to-day operations. By integrating WMS into warehouse operations, businesses can automate tasks such as order picking, inventory tracking, and stock replenishment. This leads to a more organized, accurate, and streamlined workflow, enabling warehouses to handle larger volumes with greater precision.
The WMS works by communicating with other systems, such as Enterprise Resource Planning (ERP) and Transportation Management Systems (TMS), allowing seamless coordination across the supply chain. It provides managers with detailed reports and insights, helping them to make smarter decisions that boost efficiency and reduce operational costs.
Enhancing Inventory Accuracy with WMS
One of the key benefits of implementing a WMS is the significant improvement in inventory accuracy. Traditional inventory management methods, such as manual stocktaking, are prone to errors that can lead to stock discrepancies and loss of revenue. A WMS eliminates these errors by providing real-time tracking of inventory levels, locations, and movements.
With barcode scanning and RFID technology, a WMS allows for precise tracking of products throughout the warehouse. Every movement, from receipt to storage to dispatch, is recorded and updated in real time, reducing the risk of stockouts or overstocking. This accuracy not only ensures that businesses can fulfill orders more reliably but also allows for better forecasting and inventory planning, optimizing stock levels and reducing holding costs.
Streamlining Order Fulfillment and Picking Processes
Order fulfillment is one of the most time-sensitive and critical processes in warehouse operations. WMS significantly enhances order picking and fulfillment by automating and optimizing the picking process. The system uses algorithms to determine the most efficient picking paths and the best methods for selecting items, whether that involves single order picking, batch picking, or wave picking.
By automating the picking process, WMS reduces the time it takes to fulfill orders, leading to faster delivery times and improved customer satisfaction. Furthermore, the system directs workers to the most optimal locations within the warehouse to pick items, minimizing walking time and maximizing labor productivity. This streamlining not only helps fulfill customer orders more quickly but also improves the overall throughput of the warehouse.
Reducing Operational Costs Through Automation
A WMS can significantly reduce operational costs by automating key tasks that would otherwise require manual intervention. Tasks such as inventory counting, stock movement tracking, and order picking are all automated, eliminating the need for labor-intensive processes. This reduces human error, enhances worker productivity, and lowers the cost of labor in the warehouse.
In addition, a WMS helps optimize space utilization by determining the most efficient way to store products within the warehouse. The system automatically allocates products to the best storage locations based on factors such as product size, weight, and demand. This improved use of warehouse space helps to lower storage costs and improve the overall efficiency of warehouse operations.
Improving Labor Efficiency and Productivity
Labor costs are a significant component of warehouse expenses, and improving labor efficiency is key to reducing overall operational costs. A WMS plays a central role in increasing labor productivity by providing real-time data that helps managers assign tasks more effectively. The system can track worker activity, highlight areas where workers are spending excessive time, and suggest adjustments to improve efficiency.
Furthermore, WMS can be used to optimize worker workflows by providing automated instructions for tasks. For instance, rather than relying on verbal instructions or paper-based methods, workers can receive clear directions on where to go, what to pick, and what actions to take, all through mobile devices or handheld scanners. This reduces downtime, boosts productivity, and ensures that workers are utilized to their full potential.
Enhancing Customer Satisfaction with Faster and More Accurate Deliveries
In today’s competitive marketplace, customer satisfaction is paramount. The ability to fulfill orders quickly and accurately is one of the most important ways a warehouse can meet customer expectations. By implementing a WMS, businesses can achieve faster order processing, reducing lead times and ensuring that customers receive their products on time.
A WMS also improves order accuracy, minimizing the risk of errors such as shipping the wrong product or incomplete orders. This reduces the likelihood of returns and customer complaints, ultimately improving customer satisfaction and building loyalty. Additionally, WMS integrates with customer-facing systems, allowing businesses to provide real-time order tracking, giving customers greater visibility into the status of their purchases.
Preparing for the Future with Scalable WMS Solutions
As businesses grow, so do their operational needs. A Warehouse Management System offers scalability, meaning it can evolve alongside the business to accommodate larger volumes of orders and more complex operations. Whether a business expands to multiple locations or diversifies its product range, a WMS can adapt to new requirements without requiring a complete system overhaul.
Moreover, modern WMS solutions integrate with advanced technologies such as robotics, artificial intelligence (AI), and the Internet of Things (IoT), helping warehouses stay ahead of the curve. These integrations allow businesses to implement automation, predictive analytics, and real-time data tracking on an even larger scale, further improving operational efficiency and positioning the business for future growth.
Conclusion
A Warehouse Management System (WMS) is no longer just a luxury; it is a necessity for businesses looking to streamline their operations and remain competitive in a fast-evolving market. By enhancing inventory accuracy, improving order fulfillment, and optimizing labor productivity, a WMS unlocks significant efficiencies that drive cost savings and boost customer satisfaction.
For companies aiming to enhance operational efficiency, reduce errors, and support future growth, investing in a WMS is a strategic decision that will pay dividends. With its ability to automate tasks, improve inventory management, and provide real-time insights, a WMS transforms warehouse operations, helping businesses stay ahead of the competition while ensuring they are equipped for long-term success.